Case Study
50% Reduction in Component Defect Rate with Video Analytics
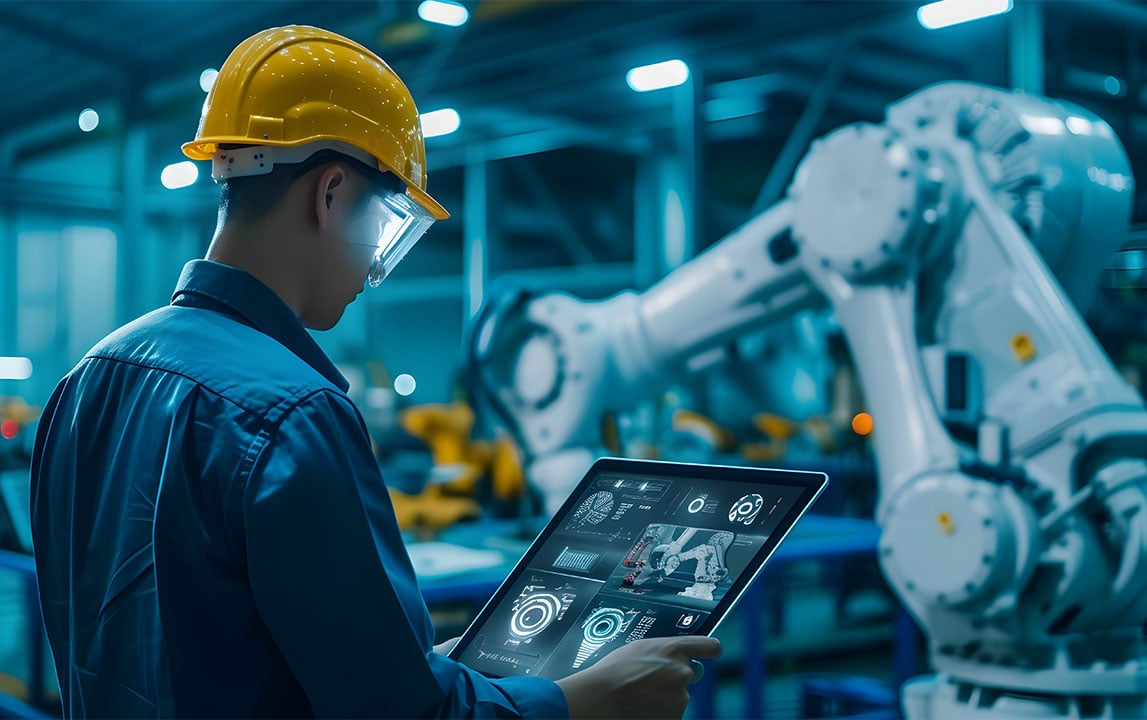
decrease in defect rates
increase in production efficiency
reduction in quality inspection cost
Background
In the dynamic world of manufacturing, the integration of AI for quality control is revolutionising traditional quality control processes. For a leading German automotive component manufacturer, the inspection of critical components such as bearings and gears, which is both time-consuming and prone to errors, posed a significant challenge.
To tackle the client’s inspection woes, Tata Elxsi helped the client to enhance their operational efficiency through AI. This solution includes intelligent video analytics and accelerated data processing, significantly reducing the time required for control processes checks and analysis.
The collaboration exemplifies the shift towards Industry 4.0, where AI-driven manufacturing solutions are essential for businesses aiming to maintain high quality control standards while optimising operations.
Challenge
Detecting minute defects is a major challenge for automotive manufacturing OEMs, as traditional inspection methods often miss critical flaws essential for safety and performance. The complexity of modern components, with intricate designs and diverse materials, complicates quality maintenance. Varying defect types require specialised detection methods.
Integrating real-time monitoring and advanced technologies in AI for quality control like machine learning and deep learning is essential yet challenging. It is crucial to balance cost management and ensuring uniform quality across production lines. Our client sought a smart automated solution to address these issues.
Solution
To address these challenges, Tata Elxsi’s AI Centre of Excellence (CoE) team proposed an advanced framework, driven by AI for Quality control, that integrates AI technologies and methodologies.
This solution focuses on:
- Utilising advanced image processing techniques on microscope-collected data for precise defect detection
- Implementing Machine Learning / Deep Learning algorithms for accurate defect classification of gears and mechanical components
- Employing real-time monitoring systems to analyse manufacturing processes
Tata Elxsi’s AI powered IRIS platform is tailored to meet unique industrial business needs. It has been instrumental in transforming the quality control ensuring consistent and reliable identification.
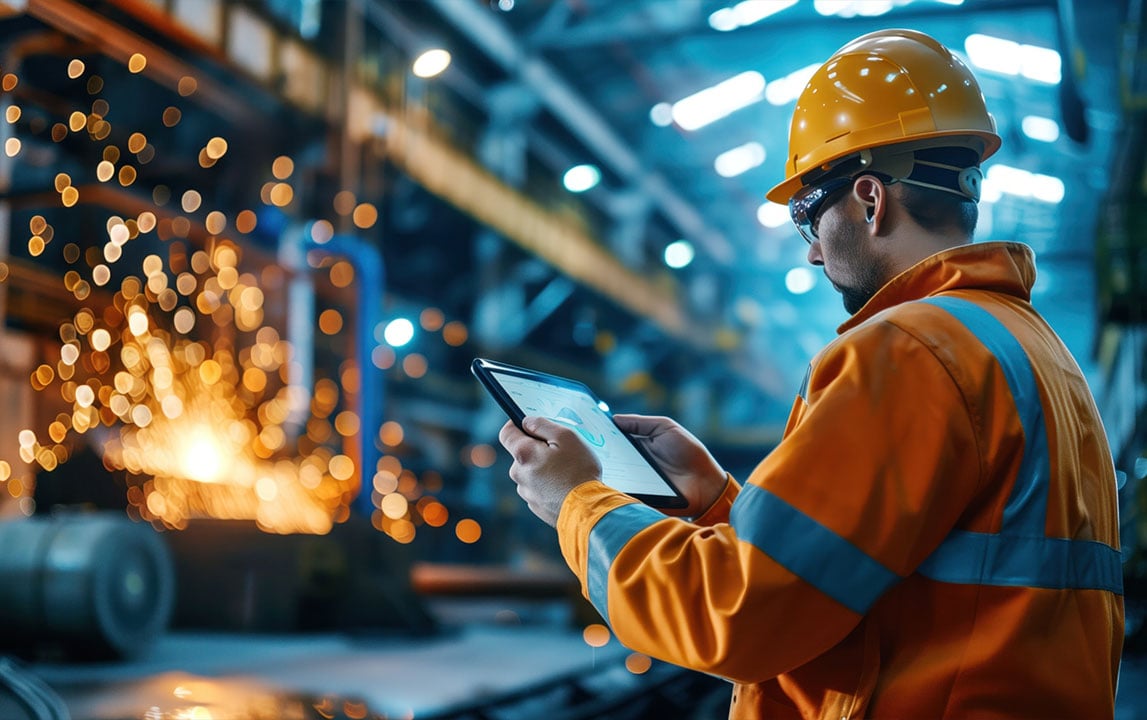
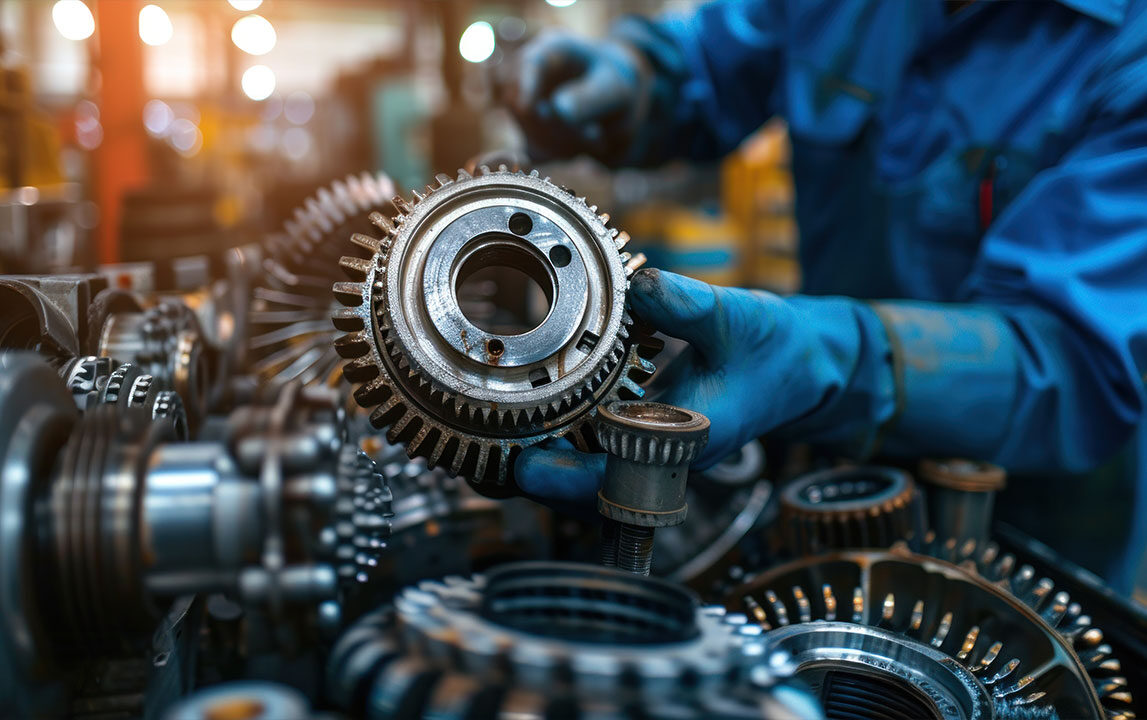
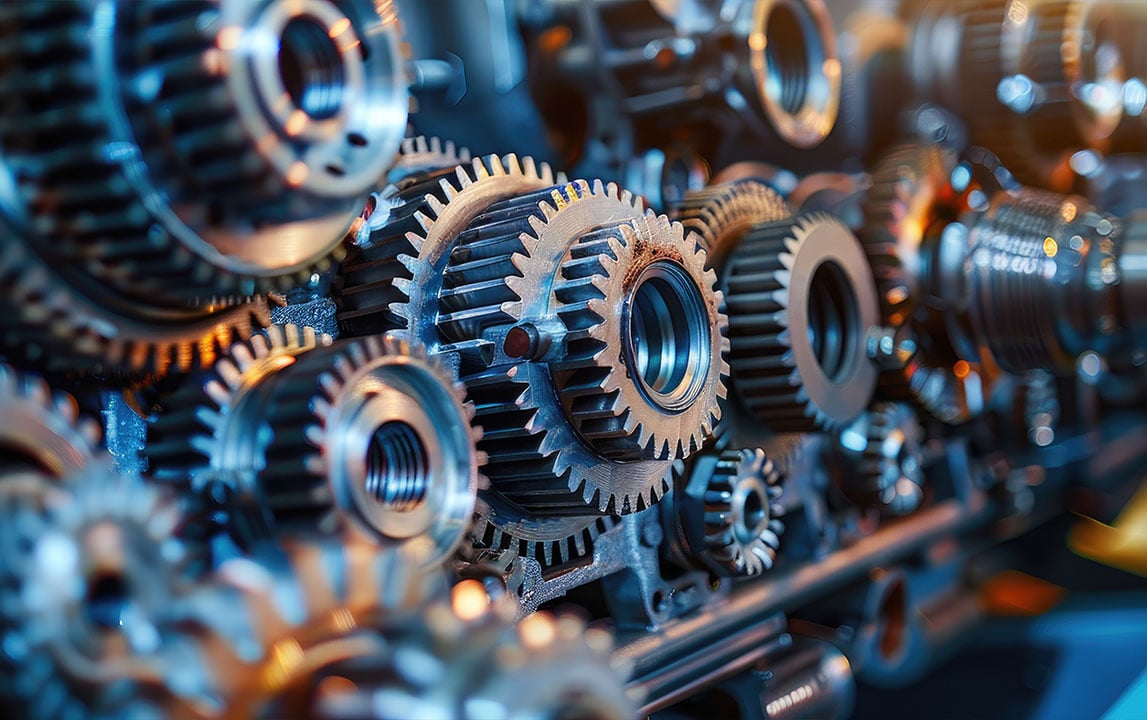
Impact
Tata Elxsi’s AI solution is tailored to meet unique business needs. It has been instrumental in transforming the quality control ensuring consistent and reliable identification.
- 50% Decrease in Defect Rates: The use of AI technology has halved the defect rates, ensuring higher quality and reliability of components.
- 35% Increase in Production: Automated defect detection has streamlined the production process, resulting in a notable increase in manufacturing output.
- 25% Cost Reduction: By reducing manual inspection efforts and improving accuracy, manufacturers have achieved considerable cost savings.
The solution driven by AI for Quality Control has drastically reduced analysis time from weeks to minutes. The client plans to expand this approach across more assembly lines and mechanical components, aiming for enhanced productivity, cost savings, and streamlined operations. The project has received positive feedback and high customer satisfaction scores (CSAT) of 4.66 and 4.51 out of 5 for the first and second phases, respectively.
Services rendered
Tata Elxsi
- Comprehensive quality assessment
- Intelligent Video Analytics Integration
- Tailored AI solution
- Ongoing Support and Optimisation
- Smart Annotation Implementation